As we all know, Bose is all about “better sound through research.” Therefore the very beginning of the supply chain starts with market and product research. This research help s to improve upon existing aspects within the sound electronic industry, as well as new ways to create exquisite sound. After all research is completed, the process continues on to raw materials in the factory. Raw materials are manipulated and transform into usable parts. The parts are then taken to be assembled, finished, and checked for overall appearance and performance quality. Next, the products are transported to their various store destinations where they await purchase.
This is the supply chain for brand new products, however select Bose locations are called Factory Stores. These stores offer both brand new as well as factory renewed, previously purchased products. Factory renewed products are those that started out brand new, but were returned during the customer’s trail period. With that said, they still go through the aforementioned supply chain process, but after being returned the merchandise goes through another process.
This chain would begin with the return of the product. After their refund is given, the product is logged onto a RA (return authorization) sheet and another form that contains defect information is enclosed in the product packaging. The product is then shipped from the store to a re-inspection factory where it undergoes intensive examination. After the product is deemed fit to look and sound exactly the same as a new product it is recertified. At this point, the product is then shipped to one of the various Bose Factory Store locations to be offered at a discounted price, at the same warranty and trial period as brand new products.
Bose® Lifestyle® 48 DVD Home Entertainment System
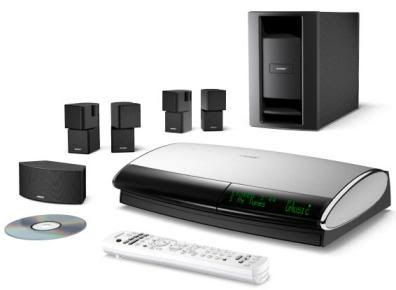
New ideas for the supply chain would include supplying more parts separately from the total package. For example, Lifestyle Home Entertainment systems come with everything a consumer needs within the box including all wiring. However, many customer move with their systems, and are unable to bring wiring with them for various reasons. Especially when the wires were installed in the walls or ceilings. However, Bose does not offer extra wiring in stores. Customers must call the customer service/technical support line. These extra parts added into the supply chain and shipped to store locations would be a great addition to the Bose experience.